A glance at modern homes reveals that LVT vinyl tiles has become a highly prefered option for flooring in nearly every rooms in the house. However, one might question how this impressive flooring choice is produced to deliver style, durability, and waterproof features. This article encourage you to continue reading to discover the manufacturing process of LVT vinyl flooring. With this knowledge, you may be inspired to learn about the LVT vinyl flooring factory production process.
The creation of vinyl tiles involves advanced printing technologies, modified composition formulas, and precise manufacturing process to provide you with stunning, high-quality, and high-performance resilient floors. Recent improvements in rigid core composition have also led to even more price attractive, durable hard surface SPC flooring products.
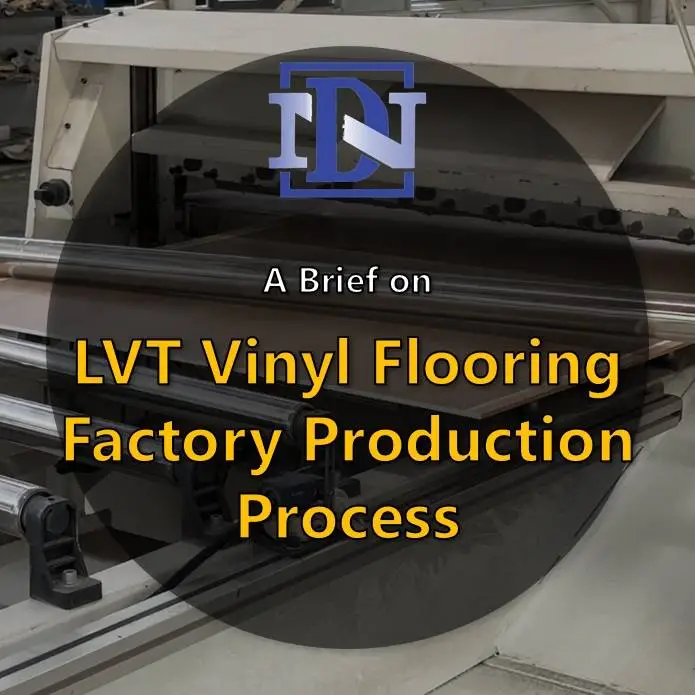
Components and Procedure
The primary composition of vinyl flooring is polyvinyl chloride (PVC) polymer, which it is modified with other compositions to deliver enhanced properties and performance in the finished LVT product. These additive compositions include stabilizers, plasticizers, pigments, and fillers. Some LVT vinyl flooring may also incorporate antimicrobial agents to inhibit the growth of bacteria and mold, an option that is frequently seen in commercial use floorings. Stabilizers are used to enhance the vinyl and reduce fading over time caused by light exposure. Plasticizers adjust the texture, making the material softer and more flexible. Pigments provide color to the flooring, while fillers can contribute to specific base core to help improve rigidity and costs. To transform PVC polymers from powder or pellet form into a finished vinyl plank, the composition needs to go through extrusion process where heat and pressure are applied to melt them into sheet form. This sheet is then pressed and adhesed to multiple layers of films to deliver desirable characteristics of the final vinyl flooring product.
Construction in Sheets, Tiles, or Planks
For conventional sheet vinyl, a thin layer of polymer composition is extruded. Depending on the required specifications, underlayer is applied to the backing. There are currently two main type of sheet vinyl flooring, the homogeneous flooring and heterogeneous flooring. These sheet vinyl flooring generally come in large rolls that can be cut to the desired size.
Vinyl tiles and planks are produced in a similar manner to sheet vinyl with the expectation that it is designed to be cutted into individual tiles. The name for “luxury” vinyl tiles refers to the fact that the LVT products are able to offer almost endless options in design patterns and colors. Due to this unique feature, LVT tiles are considered more luxurious when compare to sheet vinyl tiles.
The construction and manufacturing techniques in LVT vinyl tiles also allowed for more flexible materials and functions into the products. Various installation functions such as peel-and-stick and click-n-lock installation are developed to offer time saving installation for both consumers and project builders.
Rotogravure Printing Technique
The rotogravure printing technology has been utilized for productions for vinyl flooring products. With almost endless design possibilities,the rotogravure printing has support the LVT products to create design patterns, colors, textures that no other type of flooring can provide, except laminate flooring. This process involves a rotating print cylinder that applies different ink dyes onto the deco layer of the vinyl tile. After the printing process are completed, a transparent protective wear layer is added to the top to protect the deco layer of LVT flooring.
Prolonged Protective Wear Layer
The thickness of the wear layer is the primary factor to determine the durability of the vinyl flooring. Generally the thicker the wear layer, the longer the effective life time are for the LVT. The thickness in wear layer is measured in mils, which is roughly equivalent to the thickness of a page from a telephone book. For instance, a 10mil wear layer is similar to about 10 pages of paper. Generally, higher-priced and better-quality vinyl tends to have thicker protective wear layers, enhancing durability and resistance from damage. A robust protective wear layer also contributes to maintaining the appealing appearance of new vinyl flooring over time. Furthermore, this layer influences other important performance features such as ease of maintenance, stain resistance, scratch resistance, and anti-bacterial performances.
When LVT Flooring Starts to Lose Its Appearance
When LVT flooring starts to appear faded and dull, it’s typically due to prolonged sunlight exposure and countless scratches in the protective wear layer. Scratches trap dirt, grit, and sand, which cause additional damage. Fortunately, the protective wear layers of vinyl flooring are exceptionally strong and durable, allowing them to withstand wear and stains. This durability is one reason why vinyl flooring has become a popular choice among consumers seeking practical and attractive flooring solutions.
LVT Vinyl Flooring Factory
There are hundreds and thousands of LVT vinyl flooring factory to select from. Whether you are a flooring big box store or flooring distributor, its worth to explore different options in vinyl flooring factories. Different factories and suppliers can have different production strength and capability, so this means their product offering and quality can vary and be different.
Using Hengdi New Material Group as an example, our company strength is in composition innovation and extrusion techniques. Our current production equipments includes three extrusion system and four hydraulic thermo pressure line. While this might not seen a lot when compared to leading manufacturers with 20 to 60 extrusion lines, our R&D Innovation and Operation know-how has allowed us to offer unique and cost effective product solutions in resilient flooring category.
Our Strength Resilient Flooring Products
- Polypropylene LVT and Polypropylene SPC, offering PVC Free Resilient Flooring Solution
- Extruded Dryback LVT Tiles with Acclimation Free Dimensional Stability
- Extra Length and Extra Large Vinyl Planks upto 1800mm length
- Laminate Like Anti-scratch Resistance with 38N Coating Technology
- Silicon Loose Lay Grip LVT Flooring with 2.0mm thickness